China's Zombie Steel
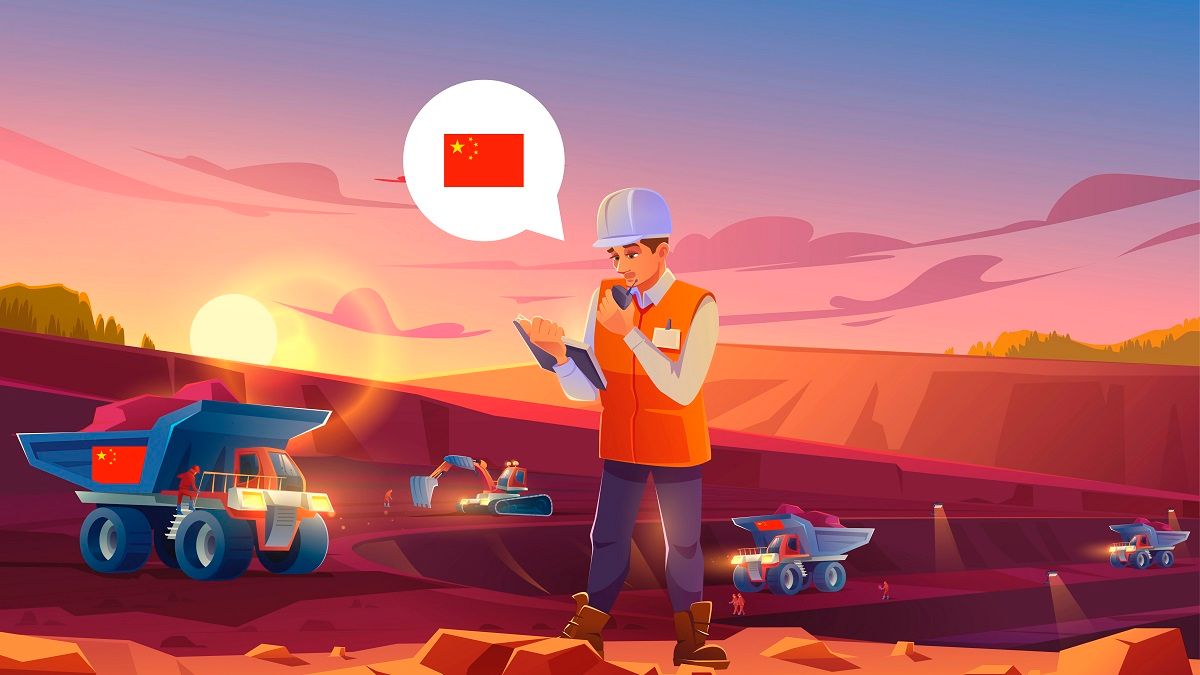
In today's Finshots we explain why China has been importing record amounts of iron ore from India.
The Story
Yesterday, there was a rather interesting news article on BloombergQuint. It read —
China’s purchases of iron ore from India rocketed to an eight-year high in the first half of 2020, fueled by supply shocks at major producers and record steel output at the world’s largest steelmaker. Shipments of the raw material from India more than doubled to 20 million tons in the six months through June from a year earlier, according to China’s customs data. It was also the highest since the South Asian country shipped out 27.8 million tons in the first half of 2012.
Now, parts of this argument do make sense. China is after all the world’s largest steelmaker. They are responsible for half of the global steel output and they need a lot of iron ore to keep meeting their lofty production targets. Also, considering the economy is slowly getting back up to speed, it makes sense to beef up the country’s iron ore stockpile right now.
Ideally, they’d be looking at Australia or Brazil to fill the supply void. But natural calamities have disrupted that equation. A dam rupture in Brazil hit the country's biggest mining company and the tropical cyclone Veronica affected production in Australia. Meaning, Chinese steelmakers have had to look elsewhere. And it seems they have turned to India.
But then this does not explain everything. After all, it’s not like demand for steel is skyrocketing at the moment. Auto manufacturers are crippled. Real Estate isn’t exactly booming either. Construction activity is yet to reach top gear. So it’s a bit weird that Chinese steelmakers are still producing ridiculous amounts of steel at a time when buyers are hard to come by.
It makes no economic sense. Until that is… You start digging a bit.
The show must go on
Most steel plants in China still use the blast furnace — a large structure that takes in hot air and converts iron ore into molten iron under extremely high temperatures. The molten iron has to be purified and shaped into cuboids before you can carve steel parts out of it. But the blast furnace is a key component of any integrated steel-making plant.
However, the whole arrangement is a bit peculiar since you don’t really turn off a blast furnace unless you’re shutting it down for good. You have to keep it running. If you don’t, the blast furnace cools down and the iron and slag that collect at the bottom turn into a solid mass.
Once this happens it’s extremely difficult to re-melt all of this stuff and start the furnace once again. In the meantime, the steel-making process comes to a grinding halt. The entire plant has to cease operations.
So even if demand for steel does not necessarily keep pace with production numbers, manufacturers are still compelled to produce steel. And this brings us back to the India equation.
India mainly exports lower grade iron ore (~58% iron content). They could export higher-quality ore, but that would attract a 30% duty and it would inevitably push prices higher. Foreign manufacturers won’t pay that kind of premium. So most domestic exporters simply stick to low-grade iron.
And since Chinese steel mills are desperately trying to keep costs low, they’ve resorted to importing large quantities of cheap iron ore from India and are currently churning out steel even if nobody really wants them. It’s a perplexing way of doing business but one that’s still pretty cost-effective. And maybe when the effects of the pandemic slowly start waning, Chinese steelmakers will finally get rid of all this excess stockpile they've been hoarding so far.
Until then…